A Comprehensive Overview to the Process and Benefits of Plastic Extrusion
In the vast world of production, plastic extrusion emerges as a essential and highly reliable procedure. Altering raw plastic into constant profiles, it provides to a myriad of markets with its exceptional flexibility.
Understanding the Essentials of Plastic Extrusion
While it might appear facility initially glimpse, the process of plastic extrusion is basically basic - plastic extrusion. It is a high-volume manufacturing strategy in which raw plastic is melted and shaped right into a constant account. The process starts with the feeding of plastic material, in the type of granules, powders, or pellets, right into a heated barrel. The plastic is then melted utilizing a combination of heat and shear, applied by a rotating screw. Once the molten plastic reaches the end of the barrel, it is compelled with a little opening called a die, shaping it into a preferred form. The designed plastic is after that cooled, strengthened, and cut into preferred lengths, finishing the procedure.
The Technical Process of Plastic Extrusion Explained
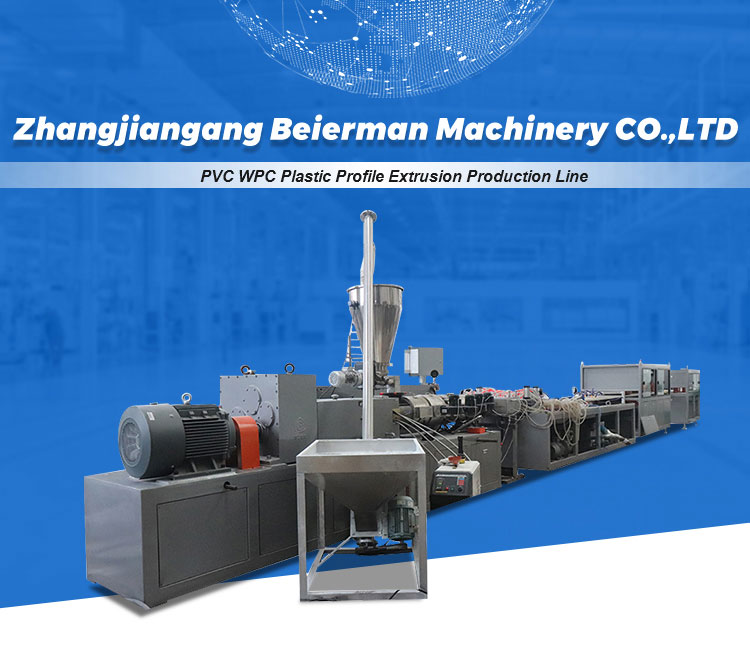
Sorts Of Plastic Suitable for Extrusion
The option of the ideal kind of plastic is an essential aspect of the extrusion process. Different plastics use unique residential properties, making them extra suited to specific applications. Polyethylene, for instance, is typically utilized due to its low expense and easy formability. It offers superb resistance to chemicals and dampness, making it ideal for items like tubing and containers. Likewise, polypropylene is one more prominent choice as a result of its high melting point and resistance to fatigue. For even more robust applications, polystyrene and PVC (polyvinyl chloride) are commonly selected for their strength and durability. Although these are common choices, the option eventually relies on the particular needs of the product being created. So, recognizing these plastic kinds can substantially boost the extrusion procedure.
Comparing Plastic Extrusion to Various Other Plastic Forming Approaches
Recognizing the types of plastic appropriate for extrusion leads the way for a more comprehensive conversation on how plastic extrusion compares to various other plastic developing techniques. These consist of injection molding, strike molding, and thermoforming. Each approach has its distinct usages and benefits. Shot molding, for instance, is excellent for creating elaborate components, while strike molding is excellent for hollow things like containers. Thermoforming excels at creating superficial or big components. Plastic extrusion is unmatched when it comes to developing constant profiles, such as seals, gaskets, and pipes. It additionally allows for a regular cross-section along the length of the item. Therefore, the option of approach greatly relies on the end-product requirements and specs.
Trick Advantages of Plastic Extrusion in Manufacturing
In the world of production, plastic extrusion provides several substantial benefits. One remarkable advantage is the cost-effectiveness of the learn this here now procedure, which makes it an economically attractive manufacturing method. In addition, this method provides remarkable product flexibility and improved production speed, therefore boosting overall manufacturing performance.
Affordable Production Method
Plastic extrusion leaps to the forefront as an economical production technique in production. This process stands out for its capability to produce high quantities of product visite site rapidly and successfully, providing suppliers with substantial savings. The key cost advantage is the ability to make use of cheaper resources. Extrusion uses thermoplastic materials, which are less expensive contrasted to metals or ceramics. Even more, the extrusion procedure itself is fairly simple, decreasing labor costs. Additionally, plastic extrusion calls for much less power than standard manufacturing techniques, adding to reduced operational expenses. The procedure additionally minimizes waste, as any faulty or excess products can be recycled and recycled, offering an additional layer of cost-effectiveness. Generally, the economic advantages make plastic extrusion a very appealing option in the production sector.
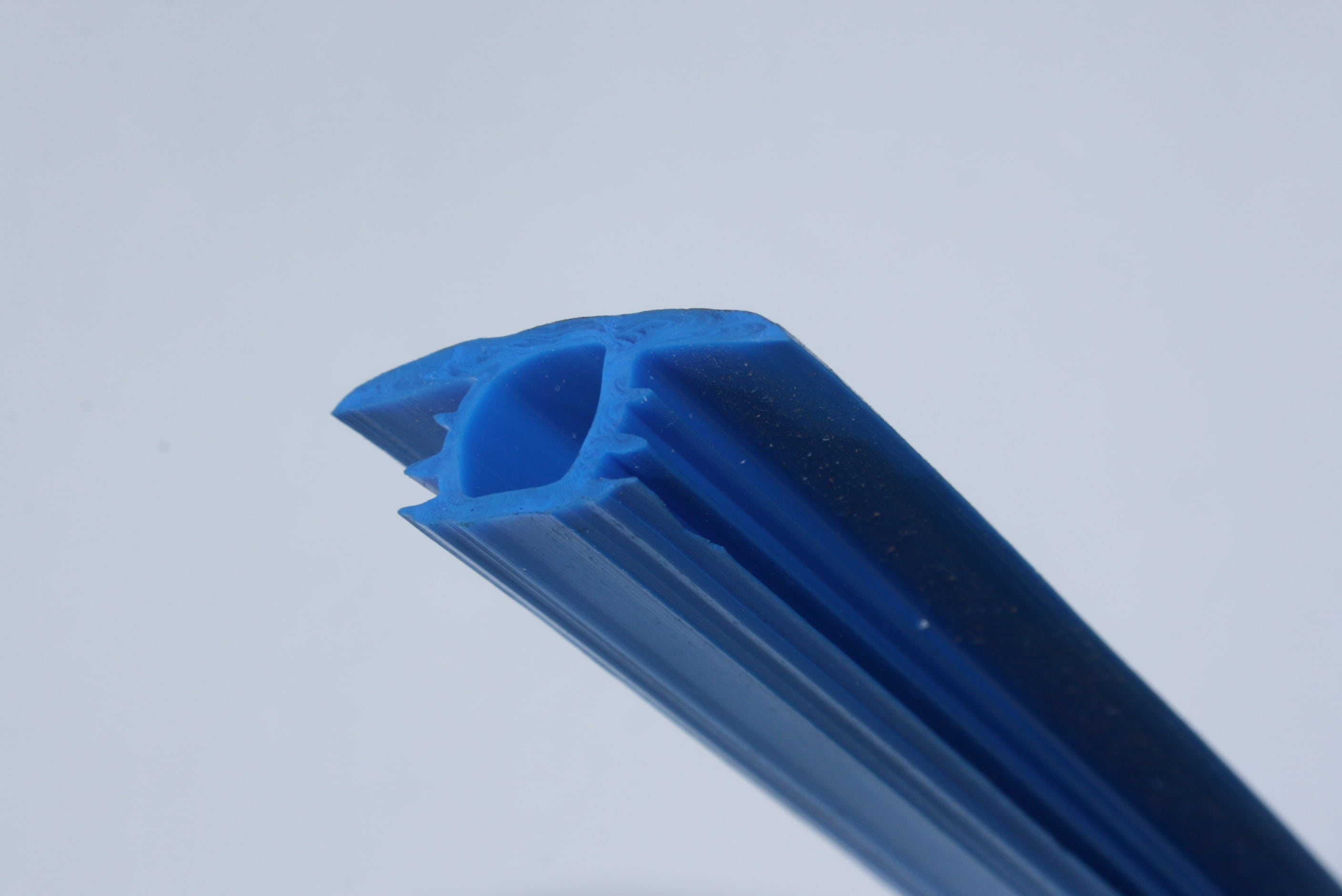
Superior Product Flexibility
Past the cost-effectiveness of plastic extrusion, one more substantial benefit in producing lies in its premium product versatility. This makes plastic extrusion an excellent solution for sectors that require personalized plastic parts, such as automobile, building and construction, and packaging. In essence, plastic extrusion's item flexibility promotes technology while enhancing operational effectiveness.
Boosted Manufacturing Speed
A considerable benefit of plastic extrusion exists in its boosted manufacturing speed. Couple of various other manufacturing processes can match the rate of plastic extrusion. Furthermore, the capability to maintain regular high-speed manufacturing without sacrificing item high quality sets plastic extrusion apart from various other approaches.
Real-world Applications and Effects of Plastic Extrusion
In the world of production, the technique of plastic extrusion holds profound significance. The economic advantage of plastic extrusion, mainly its high-volume and cost-efficient result, has revolutionized manufacturing. The industry is persistently striving for developments in recyclable and naturally degradable materials, suggesting a future where the advantages of plastic extrusion can be maintained without jeopardizing ecological sustainability.
Verdict
To conclude, plastic extrusion is a very reliable and reliable approach of changing raw materials into diverse items. It supplies countless benefits over other plastic forming methods, consisting of cost-effectiveness, high result, very little waste, and style flexibility. Its influence is exceptionally really felt in various industries such as building, vehicle, and customer products, making it a pivotal procedure in today's production landscape.
Delving much deeper into the technological procedure of plastic extrusion, it starts with the selection of the appropriate plastic product. When cooled down, the plastic is reduced into the required sizes or wound onto reels if the item is a plastic movie or sheet - plastic extrusion. Comparing Plastic Extrusion to Various Other Plastic Forming Techniques
Understanding the More Bonuses kinds of plastic appropriate for extrusion leads the method for a broader conversation on exactly how plastic extrusion piles up against other plastic developing methods. Couple of other production processes can match the rate of plastic extrusion.